wire to weld car sheet metal Welding sheet metal with a wire feed welder involves preparation, precision, and proper technique to achieve strong, clean welds. From selecting the right equipment to finishing the weld, each step plays a crucial role in the process. . Generally, sheet metal workers fabricate and install metal products using saws, lasers, shears, presses and computers. This sort of rigorous labor includes a high risk of illness.
0 · welding sheet metal with mig
1 · welding automotive sheet metal
2 · welding auto body sheet metal
3 · tig welding sheet metal videos
4 · tig welding automotive sheet metal
5 · mig welding sheet metal 101
6 · mig welding body panel videos
7 · best welding for auto body
Galvanized steel is a form of standard steel in which the steel is coated in zinc to ensure enhanced corrosion resistance. This galvanized coating protects the steel substrate from damage typically caused by moisture or temperature changes.
Are you planning to weld auto body sheet metal or any thin metal with a MIG welder or tig welder? You should keep in mind some critical things to avoid creating any unwanted situations, and we have decided to incorporate them right here. See more Learn how to MIG weld automotive sheet metal in about 5 minutes or less! I keep it short and to the point in this welding instructional video and show how very easy it is to start MIG. Flux Core Welding Sheet Metal uses gas-less flux core wire which means you don’t need gas. The wire contains “Flux” which will burn while you weld. The flux acts as a protective gas that stops the weld from becoming . MIG Welding Automotive SheetmetalThis clip from howtoASAP.com is from a 52 minute video featuring nationally recognized automotive builder, Craig Hopkins. Wh.
Welding sheet metal with a wire feed welder involves preparation, precision, and proper technique to achieve strong, clean welds. From selecting the right equipment to finishing the weld, each step plays a crucial role in the process. . Mig welding is the best method for welding car sheet metal. Apart from being affordable, . It is best to use 0.030-inch diameter flux-cored wire for car sheet metal. This particular option works for any sheet metal if its thickness level ranges from 14 gauge to 22 gauge.
The I-CAR finds it appropriate to use 0.023-inch diameter wire when repairing autos, primarily composed of sheet metal. And a 0.030-inch wire like the Forney flux-cored welding wire is suitable for welding materials that are 18 gauge thick or 4.175 millimeters. Learn how to MIG weld automotive sheet metal in about 5 minutes or less! I keep it short and to the point in this welding instructional video and show how v.
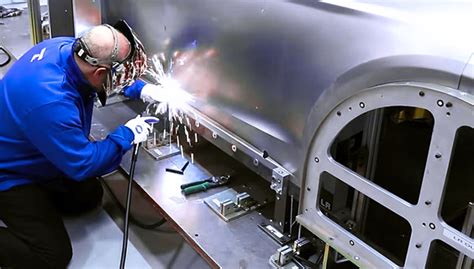
professional cnc milling machine
For thinner gauge sheet metal like 18 or 20 gauge we suggest .023 (6mm) wire in your MIG welder. Keep the Stick Out Short-Stickout of your MIG wire is important when welding any type of metal, but especially sheet metal. Holding the tip too far from the surface will cause the wire to have to come out too far to touch the metal. This means the . Never use wire thicker than the base metal because the stock will warp or burn before the wire melts. Using 0.023, 0.024, and 0.030 in MIG solid wires for sheet metal is best. . Welding sheet metal often requires a beautiful, smooth weld line. You can only achieve that naturally with a TIG welder. |Starting from scratch and setting up two different mig welders to weld sheet metal In this video I show you how to properly set up your welder settings for thin sheet metal welding on automotive car or trucks repairs for beginners.In this v.
In this video I demonstrate how to set up your mig welder so you can weld thin sheet metal. We also showed in this video how to make your pattern, fit and we.Wondering if it's possible to butt weld automotive sheet metal with a flux core welder? This video can help answer that question by using a Harbor Freig. As is always the case in MIG welding, it is critically important to match the wire type to the base metal. So if you are welding an aluminum base metal, you will need to go with an aluminum wire. . As far as flow rate goes, you should be within the range of 20-30 CFS (cubic feet per second) for welding car panels. Set the Voltage for MIG .When you MIG weld any metal sheet, you must look at and care for two things. Burning through the sheet itself. Warping of the sheet, especially the edges; Creating excess heat and burning through one part of the sheet is easy. Even the most experienced welders find it hard to control the heat. It can only be achieved with patience and practice .
Try going for a wire of .023 inches when welding sheet metal. For sheet metal, I use INE welding wire and it is just as good as their flux-cored wire, if you want, you can grab one here: https://amzn.to/37BeVJ1; While wire feed welding .
But in reality, some users are welding with the wrong polarity, are using low-quality wire, or don’t clean the base metal properly. Keep in mind that usually FCAW will work with negative or reverse polarity and don’t be cheap! Invest in .
The more you know, the more effectively you can weld sheet metal on cars, ensuring the highest quality results. Step 8: Continuous Learning and Improvement. Building your skills and knowledge in welding continues . Get the 2 pieces as close together as possible with clamps, vice grips, sheet metal screws or even dent it if you have to. Cut the mig wire flush with the nozzle every time before you start, I like to start the weld on the frame rail in the centre . Welding sheet metal with a flux core is feasible for thin materials. This process utilizes a flux-cored wire to shield the weld pool. . For welding thinner sheet metal, a 0.030″ wire can provide better control over the heat input and minimize the risk of burning through the metal. Moreover, when selecting the wire, consider: . Weld metal that is less than 6mm will have a tendency to buckle and sag over time, and it can be extremely difficult to get a good bead on the metal. Weld metal that is too thick will cause you issues as well. To avoid these issues, you will want to weld thin sheet metal with flux core. Welding thin sheet metal with flux core is a great way to .
Tack welding is the best way to hold the metal in place before you fully weld it to the original metal. Tack welds are simply small welds that barely penetrate the metal and aren’t pushed or pulled to form a bead. Tack weld different areas of the joint about an inch apart. This will hold it in place and allow you to weld it properly. Complete .
For thin sheet metal welding it can be 30 ampere while for thicker (e.g. 1/8” square groove weld)- it can go up to 220 ampere for example. GMAW-S gives low heat and makes it easy to use in all positions on sheet metal, low carbon steel, low alloy steel, and stainless steel sheet metal from 25 gauge (0.02 inch or 0.5 mm) to 12 gauge (0.1 inches or 2.6 mm).Most of the light gauge sheet metal work will require the use of .023- or .24- inch while if you have a sheet metal having a gauge of more than 18-gauge then a .030-inch wire would be the most ideal. A ER70S-6 wire would be most ideal for welding mild steel. New to the forum and I am a hobby welder. I have a HF Flux 125 that I converted to DCEN with a rectifier and 90,000mfd of capacitance to smooth it out. Noticed a huge difference in quality vs AC like the welder came. Much better "sizzle", less spatter etc. I had always been using the wire that came with the machine but read about that wire sucking.
Today, we'll explore essential techniques for welding sheet metal and roll cage tubing in your DIY hotrod project car. While these tips aren't geared toward .
The thinner wire is best for sheet metal. Because we are using an extension cord (240v), we adjusted the AutoSet wire setting to .030 wire. This tells the machine to use a higher voltage setting, which makes up for the longer power cord. . When learning how to weld sheet metal on a car, any mistakes made are smaller and therefore easier to .Place the welding tip wire at the gap and tack-weld several small spots, spacing them evenly apart. Tack in a few places, apart from each other, and wait until the panel is cool to the touch. Then tack between the two previous tacks. Avoid Warping the Sheet Metal. It's very possible to warp panels on your car while welding them in place.
welding sheet metal with mig

F2.14 F2.13 F2.12 F2.11 F2.10 C2160 C2021 C2110 C2075 C2163 F2.24 F2.25 F2.26 . Excursion, Super Duty Series F−250, F−350, F−450, F−550 ’04 11−1 Fuse and Relay .
wire to weld car sheet metal|tig welding automotive sheet metal