how to calculate the bend radius of sheet metal There are lots of different paths to find your way around a bend, by using either the included or complementary angles. We can easily calculate these values; it is the applicationof the . See more If your project needs electrical boxes or enclosures, and you don’t know what are the main types of electrical enclosures, you need to read this guide, I will tell you 76 types of electrical boxes for your business based on material, .
0 · sheet metal bending calculator free
1 · sheet metal bending angle chart
2 · sheet metal bend radius formula
3 · sheet metal bend length calculator
4 · sheet metal bend calculation formula
5 · calculating bend allowance sheet metal
6 · bending force calculator sheet metal
7 · bend radius calculator in inches
Custom fabricate a meter base cover for your home or bld. Metal dutch door shelves , kick plates of any size for doors. Door jambs of any size . Small clips of any size if you need a duplicate , bring one in And western can match it for you.
Bend Allowance (BA) BA = [(0.017453 × Inside radius) + (0.0078 × Material thickness)] × Bend angle, which is always complementary The length of the neutral axis is calculated as a bend allowance, taken at 50 percent of the material thickness. In Machinery’s Handbook,the K-factor for mild cold-rolled steel . See moreThere are two basic ways to lay out a flat blank, and which to use will depend on the information that you are given to work with. For the first method, . See more
There are lots of different paths to find your way around a bend, by using either the included or complementary angles. We can easily calculate these values; it is the applicationof the . See more The sheet metal bending radius is a critical value in sheet metal drawing that can be difficult to determine during the actual processing. This radius is dependent on the material thickness, the pressure of the press brake .
Among them are the workpiece material and thickness, the bend angle and inside radius, the method used to bend the metal (air vs. bottom bending), and the oft-misunderstood K-factor, also known as either the neutral factor or the Y-factor. Input Material Thickness and Inner Radius: • Enter the precise sheet thickness and desired inner bend radius. • The calculator will instantly .
A Rule of Thumb in Metal Bending. There’s a rule of thumb to determine a steel’s minimum bend radius, and this generally works for aluminum too: Divide 50 by the material’s tensile reduction percentage as specified by . Use SendCutSend’s bending calculator to input your desired material and the units of measurement for your design to get the calculated bend allowance and bend deduction for your part before sending it to our lasers. .
In this Tech Tip, we will explore the various bend calculation options available for sheet metal, namely K Factor, bend allowance, and bend deduction, and guide you on when to use each.
To calculate bend allowance: Obtain the properties of the bend (bend radius, angle, and method used). Obtain the characteristics of your material (thickness and K-factor for this specific bend). Input everything into the bend .Minimum Flange and Minimum Hole. We’ve broken down our minimum bend radii into two values: minimum hole distance and minimum flange distance. Minimum hole distance specifies how .This tool allows you to determine tonnage, internal radius, V-die opening and minimum flange. You just have to insert the characteristics of the sheet metal to be bent. The tool can calculate .Assuming you used an inside bend radius smaller than the material thickness, the K-factor (or neutral factor, if you prefer) in our cheesy example would be 0.33 for an air bend and 0.42 for a bottom bend, both gradually increasing to 0.5 for .
How is the bend radius calculated for sheet metal? The bend radius for sheet metal can be calculated using a simple formula. It is typically expressed as a multiple of the material thickness. To calculate the bend radius, multiply .
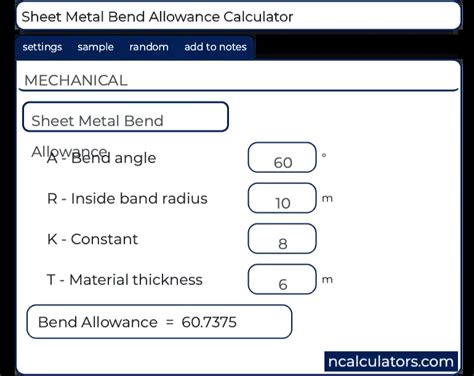
metal rosary boxes
sheet metal bending calculator free

We are going to review three bending scenarios with three different bending angles; 60, 90 and 120, and we will calculate K-Factor, Bend Allowance and Bend Deduction for them. The bending tool has a radius of 30 mm which .Our Sheet Metal Bend Calculator takes into account the material thickness, bend radius, bend angle, and K-factor to provide accurate bend allowance and bend deduction values. This ensures your bends are accurate, minimizing errors and optimizing material usage.
How to calculate the value of material shrinkage. With this free online tool we quickly get the sheet metal bend deduction, and therefore the sheet metal blank initial flat length, from the finished part measurements. You only have to insert interior angle, flange lengths, K factor, inside radius, and material thickness. So in this case, a 0.472-in. die opening will give you a 0.0755-in. floated inside bend radius on the part. When your die opening changes, so does your inside radius. If the die opening is 0.551 in. (0.551 × 0.16), the inside bend radius changes to 0.088; if the die opening is 0.972 in. (0.972 × 0.16), the inside bend radius changes to 0.155. We generated the following bend allowance chart using the sheet metal bend allowance calculator for steel, assuming the K-factor of 0.45, bend angle of 90 degrees, and inside radius of 0.05 inches (1.3 mm). The actual K-factor may depend on the type of bending operation, the thickness of the sheet, and the material.
Several terms are at the heart of any sheet metal bending operation, including the neutral axis, inside bend radius, outside setback (OSSB), and bend allowance (BA). You calculate the bend deduction by doubling the OSSB and subtracting the BA.
How to calculate tonnage, internal radius and other bend parameters. This tool allows you to determine tonnage, internal radius, V-die opening and minimum flange.You just have to insert the characteristics of the sheet metal to be bent.The bending radius is the radius from the start point of the bend to the center of the bend in plastic working of a metal or other sheet, pipe, or rod by pressing or rolling. Each material has a limit for bending without fracture which is determined by its thickness or diameter. As the bend angle gets wider, the circle needs to get larger to conform to the bend shape; a larger circle, of course, has a larger radius. This is how we measure the inside bend radius in precision sheet metal fabrication. The smaller the radius, the sharper the bend’s curve; the larger the radius, the wider the curve.
Q: In a previous Bending Basics article, you mention a “material’s tensile reduction percentage” used for calculating the minimum inside bend radius of various metals. You described a rough rule to find a steel’s minimum bend radius: Divide 50 by the material’s reduction percentage, as specified by the material supplier, subtract by 1, and then multiply by the plate . Question: My co-workers and I have been reading your columns to help us understand what tooling our shop will need to avoid overstressing our materials with small dies. We air bend our 0.125-inch-thick 5052-H32 aluminum with a 1-mm punch and 16-mm die. Based on your columns, the inside bend radius should be 13 to 15 percent of the die opening.
How To Calculate Bend Radius. Calculating the bend radius for different metals involves understanding the material properties and the specific parameters involved in the bending process.Bend radius is critical in metalworking, particularly in the fabrication of components such as sheet metal parts, where excessive bending can lead to material failure.
K-factor in sheet metal is a constant used to calculate sheet metal bend allowance, bend deduction, Flat length and Neutral axis position. . Mathematically outside setback is equal to the product of the sum of sheet . Calculating Bend Allowance using Empirical Formulas. Once the material thickness and bend radius are known, the bend allowance can be calculated using empirical formulas. One common formula is the K-factor method, which considers the material type and the bend radius. The K-factor is a constant that varies with the material and bend radius.
sheet metal bending angle chart
Factors Influencing the Minimum Bend Radius. The minimum bend radius of the sheet metal is affected by several factors, each of which is of specific importance in determining the most desirable degree of bend that would prevent collapse or paper deformation. tAng factors include:. Material Type: Different materials have varying levels of ductility and tensile strength, . Here you can specify many of the sheet metal specific properties including bend radius, K-factor, and bend relief dimensions. These can be fixed values or formulas based on the material thickness. (Note: you can find all of this information for your chosen material and thickness in our bending calculator as well.) Bend Radius Defined. The bend radius is the radius of the arc created after bending the sheet metal. It can be measured from either the inside or the outside of the bend. If the radius is too small, the metal could crack, break, or deform, ruining the product. The smaller the bend radius, the more severe the curve of the bend. Metals with small .
For a sheet metal stock with inch thickness, determine the minimum tool radius for both the steel and aluminum alloys that will not tear the material. Assume the sheet of material is in pure bending (i.e., no additional tension is applied during forming). I have already learned about the following formulas: R = 1/k; k(y) = e(y) / (h/2) e(y) = k.yQuick calculation of the angle of a radius bend However, many consecutive bends can cause an accumulation of errors, both in terms of the final angle and the radius of the bend. For this reason, it is important to rely on a press brake with a very precise backgauge and .Bending Radius Bending Radius refers to the minimum radius that can be applied to a sheet metal component where its flange originates from. Bending radii are usually dictated by available tooling, and for quick and effective design work it is recommended to speak with manufacturers so that design can be done around their standard operating procedures as well as available tooling. A big driver behind this is the use of the term “minimum bend radius” on many drawings, and how that term is interpreted. Many see “minimum bend radius” and reach for the sharpest punch they have, the one with the smallest punch tip radius. The minimum bend radius is a function of the material, not the radius on the punch.
Dialing in the k-factor for bending sheet metal parts The k-factor matters, but metal fabricators shouldn't overlook the tooling and bending method . (BA), which gives us the arc length of the shifted neutral axis after bending. To calculate an accurate BA, you need to know the inside bend radius your operators are actually achieving, which . The k-factor is fundamental in the press-bending sector and is closely linked to the concept of spring back. It is also known as bend allowance and serves to calculate the sheet metal layout. Knowing the k-factor formula is essential in order to bend any kind of sheet metal correctly; in fact, it varies according to the type of material to be deformed. .I would start with the strength of the material and calculate what strain it can tolerate without yielding. Then you can use the thickness of the sheet and the radius to see how much strain is on the outside of the sheet at a given radius. Keep the strain on the outside lower than the yield and it should stay in the elastic region.
The bend allowance and bend deduction are two measures that relate the bent length of a piece of sheet metal to the flat length. The bend allowance describes the length of the neutral axis between the bend lines, or in other words, the arc length of the bend. Therefore, the bend allowance added to the flange lengths is equal to the total flat .
metal safe box
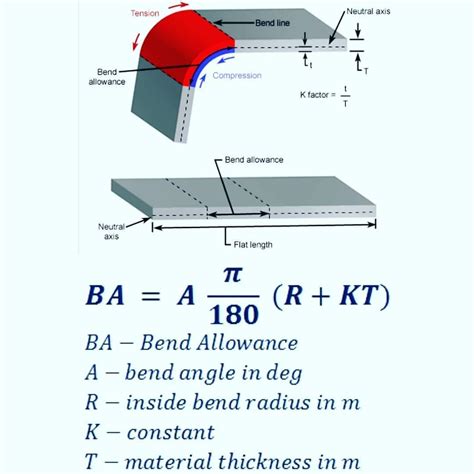
Heating Contractors in Aurora, CO. See BBB rating, reviews, complaints, & more.
how to calculate the bend radius of sheet metal|sheet metal bend length calculator